Flatwork Concrete Cost: Comprehensive Pricing Guide and Key Factors Explained
Flatwork concrete is a fundamental element in modern construction, used in projects like driveways, patios, sidewalks, and foundations. Understanding its cost is crucial for homeowners, business owners, and facility managers when planning budgets and verifying project feasibility. This guide explains what flatwork concrete is, the factors affecting its pricing, and provides cost estimates for various projects.
What is Flatwork Concrete?
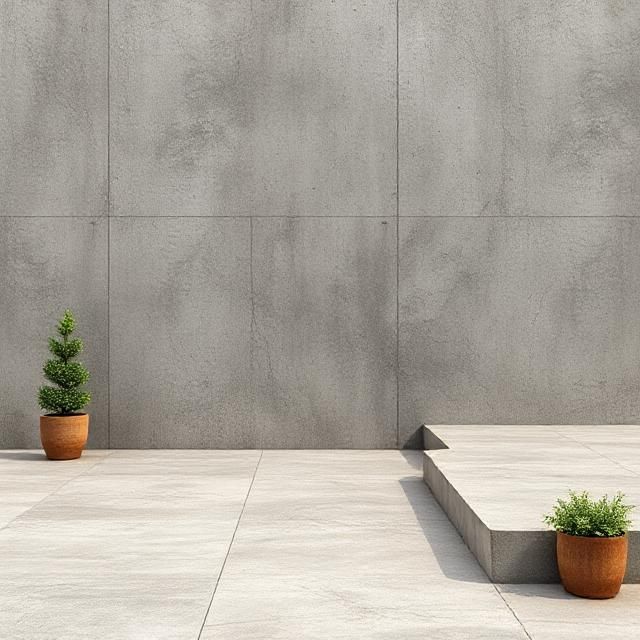
Flatwork concrete refers to poured horizontal surfaces such as patios, driveways, sidewalks, and concrete slabs. Its cost matters because it affects the overall project budget, the durability and appearance of a property, and the project's structural integrity. Factors like material quality, labor, and design complexity determine the final expense, making careful evaluation essential to avoid unexpected costs.
Services typically include the installation of concrete patios, driveways, sidewalks, and foundations. This process encompasses site preparation, forming, pouring, finishing, and curing. Many companies offer turnkey solutions—from excavation to final finishes—to ensure durability and compliance with local building codes.
High-quality flatwork improves residential curb appeal and property value through attractive patios and driveways. In commercial settings, robust concrete slabs provide long-lasting flooring for warehouses, parking lots, and other facilities while meeting safety and building code requirements. Additionally, proper flatwork helps protect against water damage and contributes to overall structural sustainability.
What Are the Main Factors That Influence Flatwork Concrete Cost?
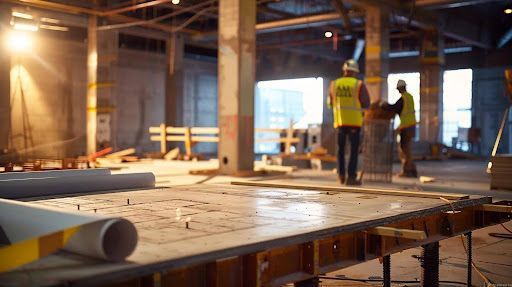
Several factors influence the cost of flatwork concrete. Evaluating these elements according to the project's scale and local market conditions helps prevent cost overruns.
Material Costs
Material costs include cement, aggregates, water, and additives like fibers or admixtures. High-quality portland cement provides durability but is pricier. Additional components, such as reinforcement mesh and vapor barriers, further increase material expenses and enhance longevity. The concrete mixture composition affects both price and performance, with specialized additives for climate resistance adding to project costs.
Labor Costs
Labor costs cover stages from site preparation to finishing touches. Skilled workers are essential for proper leveling, rebar installation, and finishing techniques. In areas with labor shortages, higher wages can significantly drive up the overall cost. Tool rental and pump truck fees for concrete delivery also factor into the total labor expense.
Permit Fees and Local Regulations
Permit fees and local building codes add expenses by requiring inspections and adherence to strict safety standards. Municipalities often mandate permits even for small projects, and failing to secure approvals can lead to fines or redesign costs. Specific concrete mixes or finishes may be required by regulation, further impacting pricing.
Additional Costs
Additional expenses include site preparation, rental of mixers, transportation fees, and contingency budgets. Environmental fees for excess materials and delays due to weather or regional economic factors can also raise project costs. Drainage systems, subbase preparation with gravel, and demolition of existing surfaces add to the overall budget.
Cost Breakdown by Project Type
The cost of flatwork concrete varies based on project type, size, and design complexity. The estimates below offer a benchmark for budget planning.
Concrete Patios
Concrete patios generally cost between $6 and $12 per square foot. This price covers materials, labor, and finishing treatments. Decorative concrete elements like stamped patterns and custom features (e.g., borders or integrated seating) can push costs to the higher end of the range. Fire pit installations and accessibility features may require additional investment.
Concrete Driveways
Concrete driveways typically range from $8 to $15 per square foot. Costs depend on driveway thickness, reinforcement, and design details. Due to exposure to weather, traffic, and road salts, driveways require robust construction and proper drainage, which can drive up the price. Reinforced concrete with steel mesh or rebar adds strength but increases costs per cubic yard.
Concrete Sidewalks
Sidewalks cost around $5 to $10 per square foot. Although smaller in size than driveways, proper sub-base preparation and quality materials remain crucial. Adherence to accessibility standards or the addition of decorative edging may further increase the cost. Curb integration and connection to existing hardscape elements require careful planning.
Concrete Foundations
Foundations are a higher investment, typically ranging from $100 to $200 per square foot. This is due to the need for precision, reinforcement, and sometimes specialized techniques like insulated concrete forms (ICFs) and vapor barriers, which are critical for building stability. Basement floors, crawl space foundations, and garage foundations each have specific requirements affecting price.
Concrete Slabs
Basic concrete slabs for sheds, garages, or other structures typically cost $4 to $8 per square foot. The thickness measured in inches, reinforcement requirements, and climate considerations all impact the final price. Floor slabs may require additional finishing techniques like broom texturing or specialized paint applications.
What Are the Different Concrete Finishes and Their Cost Implications?
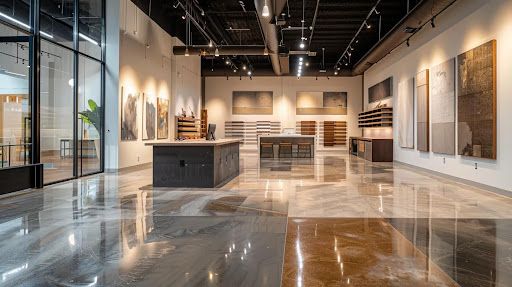
Reinforced Concrete
Reinforced concrete incorporates steel rebar or wire mesh to provide additional strength. This type is essential for structural applications like retaining walls, foundations, and heavy-duty driveways. The steel reinforcement increases costs by $1-3 per square foot but provides superior durability.
Precast Concrete
Precast concrete elements manufactured off-site can reduce on-site labor costs but may require special equipment for installation. These components work well for standardized applications like curbs, walls, and decorative elements.
Asphalt Concrete
While different from traditional concrete, asphalt concrete offers an alternative for driveways and roads. It typically costs less initially but may require more frequent maintenance compared to standard concrete surfaces.
Concrete Finishes and Their Cost Implications
The finish applied to flatwork concrete affects both aesthetics and durability. Different finishes come with varying cost implications based on labor intensity and material additives.
Stamped Concrete
Stamped concrete, which mimics the appearance of natural stone, brick, or tile, can cost 15% to 50% more than standard flatwork. The extra labor, specialized tools, and coloring agents justify the higher price by delivering enhanced visual appeal and potential resale value. This decorative concrete option works well for patios, driveways, and walkways.
Exposed Aggregate Concrete
Exposed aggregate concrete involves removing the top layer to reveal natural stones, costing 10% to 20% more than standard finishes. The detailed labor required to achieve the desired texture and slip resistance is reflected in its increased price. Sand and gravel aggregate choices affect both appearance and cost.
Colored Concrete
Adding pigments to create colored concrete generally increases costs by an additional 10% to 20%. Although more expensive, colored concrete enhances curb appeal and can complement specific design themes, adding overall value to the project.
Broom Finish
A broom finish provides texture and slip resistance at minimal additional cost. This practical finish works well for driveways, sidewalks, and other areas where safety is a priority.
Estimating Flatwork Concrete Costs
Accurate cost estimation involves combining quantitative data with on-the-ground insights. Using robust tools and consulting local experts ensures that cost projections are realistic and comprehensive.
Calculation Tools and Methods
Concrete cost calculators, detailed spreadsheets, and software programs that consider factors like material prices, labor rates, project dimensions, thickness, and reinforcement are useful. Cost data from recent projects provides valuable benchmarks for budget planning. Additionally, gathering on-site quotes and consulting local suppliers ensure accurate budget planning.
Project Size and Design Influence
Larger projects may benefit from bulk discounts but often require extensive preparation such as grading and sub-base installation. Unique design elements, such as curved edges or decorative borders, increase the need for skilled labor and additional materials, refining the overall cost estimate. Square footage calculations must account for waste and cutting requirements.
Money-Saving Tips
To save costs, compare bids from multiple contractors, schedule work during off-peak seasons, and consider standard finishes rather than custom decorative options. Efficient site preparation can also reduce future repair needs, ultimately lowering maintenance expenses. Home improvement projects bundled together may qualify for volume discounts.
Common Cost Considerations
Per Square Foot vs. Cubic Yard Pricing
Concrete flatwork typically costs between $5 and $15 per square foot, depending on design, local labor rates, and material specifics. For thicker applications, pricing may be calculated per cubic yard, with ready-mix concrete averaging $100-150 per cubic yard. Understanding both pricing methods helps in comparing contractor quotes.
Price Variation Factors
Prices can fluctuate due to material quality, labor intensity, market demand, weather impacts, and the complexity of finishes such as stamped or colored overlays. Local economic conditions, fuel costs for truck delivery, and seasonal demand all play significant roles in final pricing.
Additional Fees
Additional fees may include permits, delivery charges, site preparation, waste removal, and sealing after installation. Pump truck fees for difficult access areas, tool rental, and disposal fees for demolition debris should be included in the budget. A contingency of 10-15% is advisable for unexpected costs.
Installation Timeline and Cost Impact
Installation generally takes one to three days depending on project scope. While quicker projects may cost more due to premium labor rates, delays caused by weather or other issues can increase overall costs through extended equipment rentals and labor mobilization. Climate conditions significantly impact curing times and scheduling.
Why Choose a Local Contractor Like Dynamic Concrete For Flatwork?
Local contractors offer familiarity with regional codes and weather challenges. Their established supplier relationships can help secure competitive pricing, and their expertise in local permitting minimizes delays and unforeseen costs.
Get Your Free Flatwork Concrete Quote Today
Ready to start your flatwork concrete project? Don't let cost uncertainty delay your plans. Contact Dynamic Concrete today for a free, detailed quote tailored to your specific project needs. Our experienced team will assess your site, discuss your design preferences, and provide transparent pricing that fits your budget. Whether you're planning a new driveway, patio, sidewalk, or foundation, we deliver quality workmanship that stands the test of time. Call us now or request your free estimate—your dream concrete project is just one phone call away!
Final Thoughts
Flatwork concrete plays an essential role in construction projects and requires careful planning and precise budgeting. This guide has outlined the main cost factors, from material and labor expenses to local market variables, while providing practical tips for estimating and managing costs. By understanding each aspect—from patios and driveways to decorative finishes—you can make informed decisions to enhance project quality and avoid budget overruns. Engaging a reputable local contractor such as Dynamic Concrete further ensures that your project meets quality standards and local regulations.
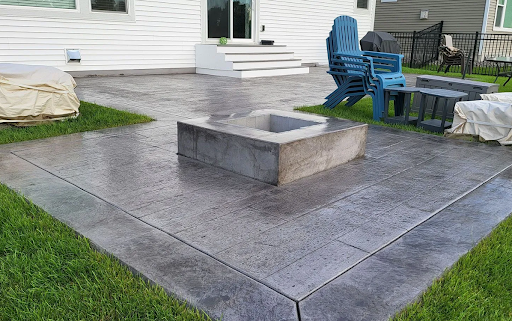
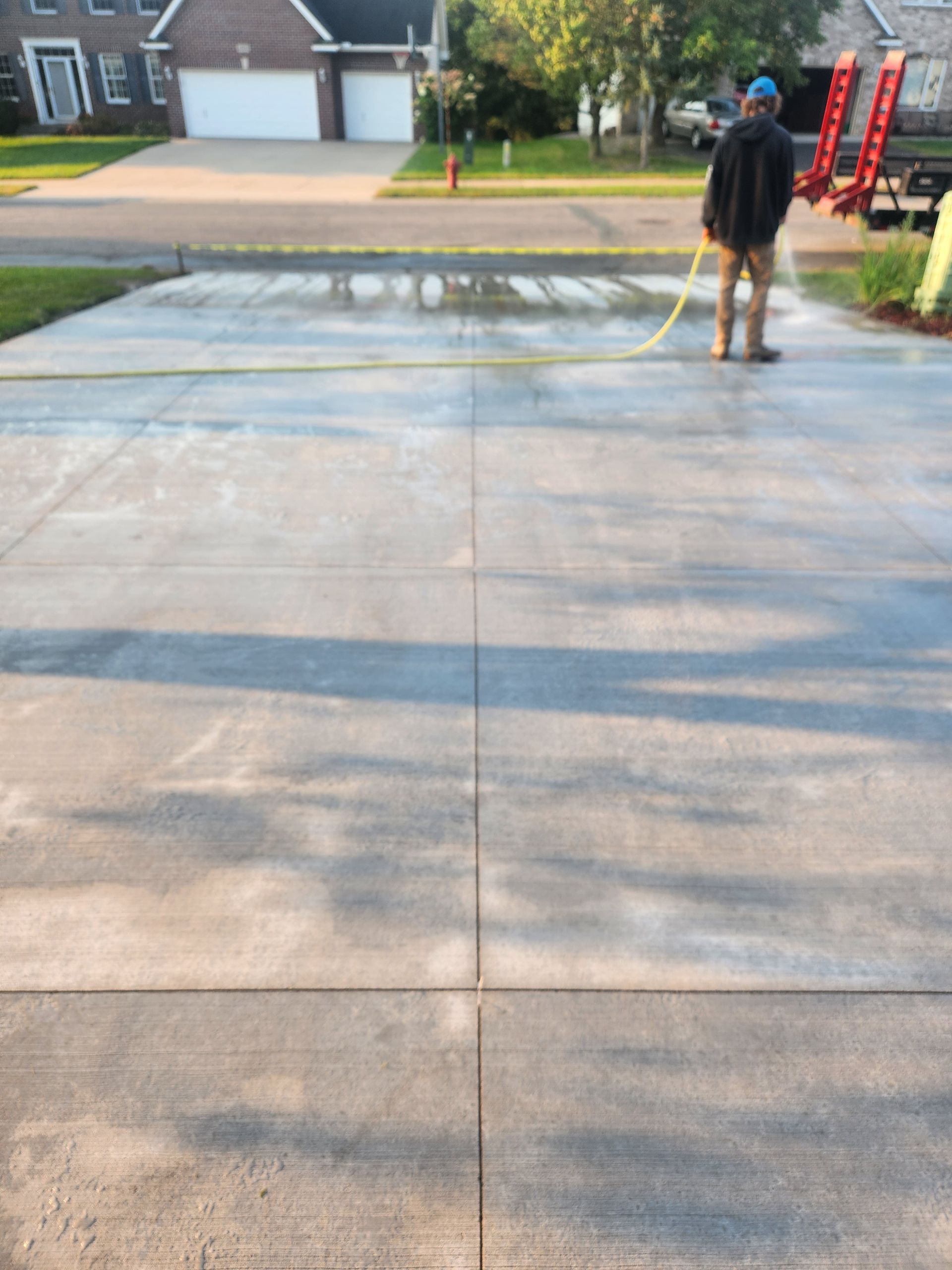